Category
- Products
-
- Solar Energy
- FAQ
- Solar Photovoltaic
- Contact us
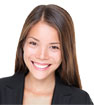
Inverter manufacturer


Inverter DV/DT effect
No easy answer on dv/dt, delta volts/delta time, change in volts/change in time, effect on bearing currents. There is still a lot of research being done on it. As a rule the quicker the voltage rise the more motor problems you may have. But the quicker the voltage raise the less heat loss across the IGBT so the more efficient the frequency inverter, smaller components and heat sink and less cost. One fairly recent way to have it both ways is to have a constantly changing carrier frequency. This makes the fast rise time of the new IGBTs appear to be sloped to the motor. This is more important on the first pulse of each half wave.
The capacitance between the inner race and outer race changes with the rpm of the motor because of the varying resistance/insulation of the grease film. Determining the Cb of a motor would be a great technical topic but probably not much value outside of a lab.
The extremely rapid voltage rise at each pulse in a pwm wave is called dv/dt. It is a significant problem as it can be a very big number. There is capacitance between the motor shaft, bearings and ground. The equation for this bearing current (ignoring complex line impedances) is I=C*dv/dt. So the faster the frequency inverter the more bearing currents will be a problem. A good dv/dt filter will help. This is not directly related to carrier frequency but can be related. Bearing currents can happen at any carrier. A sine wave filter will greatly reduce if not eliminate the problem but it is an expensive solution.
Additional complications can arise from long lead runs to the motor from an inverter coupled with the fast dv/dt can cause standing waves and voltage doubling, (typically in the range of 500 to 1000 feet) causing 1300 or more volts at the motor. (DC Bus Voltages for 480 vac volt systems average 650vdc) This requires a motor voltage insulation system that can withstand 1600 volts or more.
The capacitance between the inner race and outer race changes with the rpm of the motor because of the varying resistance/insulation of the grease film. Determining the Cb of a motor would be a great technical topic but probably not much value outside of a lab.
The extremely rapid voltage rise at each pulse in a pwm wave is called dv/dt. It is a significant problem as it can be a very big number. There is capacitance between the motor shaft, bearings and ground. The equation for this bearing current (ignoring complex line impedances) is I=C*dv/dt. So the faster the frequency inverter the more bearing currents will be a problem. A good dv/dt filter will help. This is not directly related to carrier frequency but can be related. Bearing currents can happen at any carrier. A sine wave filter will greatly reduce if not eliminate the problem but it is an expensive solution.
Additional complications can arise from long lead runs to the motor from an inverter coupled with the fast dv/dt can cause standing waves and voltage doubling, (typically in the range of 500 to 1000 feet) causing 1300 or more volts at the motor. (DC Bus Voltages for 480 vac volt systems average 650vdc) This requires a motor voltage insulation system that can withstand 1600 volts or more.
Post a Comment:
You may also like: