Category
- Products
-
- Solar Energy
- FAQ
- Solar Photovoltaic
- Contact us
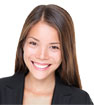
Inverter manufacturer


Home » Frequency inverters
The upsizing of the frequency inverter is only applicable to using a 3 phase inverter on single phase rather than a single phase inverter, and has to do with the diode front end. The 3 phase bridge is designed supply input power, and current in 3 phases and now you will only has 1. So the diodes are note sized for that-thus most of the time you have to derate the inverter from its rated output.
Could get an inexpensive 3 phase inverter and modify the bridge. With some luck you may find one in need of repair, with a damaged front end for cheap and rework it. The output section would be the same.
Could get an inexpensive 3 phase inverter and modify the bridge. With some luck you may find one in need of repair, with a damaged front end for cheap and rework it. The output section would be the same.
The main thing is to properly tune the frequency inverter. Personally, I would not trust autotune, especially if you are going to use a motor with 6 or more poles. Get a motor map from the manufacturer and have a competent tech tune it or get the programming from the factory application engineers.
I like the approach of using a low speed motor vs. a higher speed with a gearbox. Gearboxes are really inefficient and add mass and volume to the application. Frequency inverters are so good these days that doing it your way should be a fairly simple matter.
I like the approach of using a low speed motor vs. a higher speed with a gearbox. Gearboxes are really inefficient and add mass and volume to the application. Frequency inverters are so good these days that doing it your way should be a fairly simple matter.
The single phase inverter actually does more than just convert from 1 phase power to 3 phase power supply. The inverter controls the output waveform to allow the speed to be controlled by changing the frequency to the motor from 0-200Hz. The normal power frequency is 50Hz, so the frequency inverter actually allows you to over speed the motor if desired. With full control of the motor speed, you have direct control of the load, enabling manual or automatic control of a process, such as water pressure or flow. The frequency inverter also has total control over the rate which a motor accelerates and decelerates, providing a smooth controlled soft start and soft stop.
For extended ride-through capabilities, some frequency inverter manufacturers connect a battery bank (in place of extra capacitors) across the dc bus to sustain operation during a power outage.
In the frequency inverter industry, two main factors define power-loss ride-through capability. One value establishes the duration for maintaining a specified motor torque and machine operation. The other is the duration for maintaining control power for the logic and other control devices. In some applications, it may be advisable to select a system with the capability to maintain full torque for say 10 msec and control power for 50 msec. Others may need control power only for 20 msec to initiate an orderly shutdown and the motor coasts to rest.
In the frequency inverter industry, two main factors define power-loss ride-through capability. One value establishes the duration for maintaining a specified motor torque and machine operation. The other is the duration for maintaining control power for the logic and other control devices. In some applications, it may be advisable to select a system with the capability to maintain full torque for say 10 msec and control power for 50 msec. Others may need control power only for 20 msec to initiate an orderly shutdown and the motor coasts to rest.
Frequency inverters are widely used throughout industry to provide adjustable speed control of ac motors. Although modern versions are relatively simple to install and operate, frequency inverters are quite complex, containing a myriad of advanced hardware and software. Frequency inverter implementation and operation can often be improved by understanding internal frequency inverter basic processes. To that end, we present the terminology used to describe frequency inverter internal operations and external interfaces. This lesson contains 40 of the most important frequency inverter terms for today's design engineers.
Before looking at methods for troubleshooting frequency inverters, let's review what a frequency inverter is and how it works. A frequency inverter is a power conversion device. It converts fixed frequency sinusoidal alternating current (AC) voltage input, to direct current (DC) voltage, and then to variable-frequency AC voltage, which ultimately controls the speed of induction motors.

A frequency inverter consists of three elements: rectifier, DC bus, and inverter. The rectifier converts incoming AC power into direct current (DC) power, which is then stored on a DC bus capacitor. The capacitor's function is to reduce the AC ripple and to store the power from the rectifier. The final element of the frequency inverter is referred to as an inverter. The inverter contains transistors that deliver power to the motor. Today, most frequency inverters use insulated gate bipolar transistors (IGBT). IBGTs create an AC waveform using pulse width modulation (PWM) to switch the DC bus voltage on and off several thousand times per second. The resulting variable-frequency AC precisely controls the power delivered to the motor.

A frequency inverter consists of three elements: rectifier, DC bus, and inverter. The rectifier converts incoming AC power into direct current (DC) power, which is then stored on a DC bus capacitor. The capacitor's function is to reduce the AC ripple and to store the power from the rectifier. The final element of the frequency inverter is referred to as an inverter. The inverter contains transistors that deliver power to the motor. Today, most frequency inverters use insulated gate bipolar transistors (IGBT). IBGTs create an AC waveform using pulse width modulation (PWM) to switch the DC bus voltage on and off several thousand times per second. The resulting variable-frequency AC precisely controls the power delivered to the motor.
Briefly, a frequency inverter has the following important advantages:
- Over-current protection, especially useful while controlling motors with high inertia.
- Constant torque ensures wider range of speed control, enabling an energy efficient control throughout the range.
- The frequency inverter acts as a barrier in between all input voltage disturbances like harmonics, ripples, sags, surges, etc., and obstructs them from entering the motor.
Due to industrial standards and regulations there are not many disadvantages to frequency inverters. Most high quality frequency inverters comply with all these standards and regulations. Manufacturers improve their products with ongoing research and development programs. To eliminate any disadvantages, frequency inverter manufacturers will also advise users of how to install and operate their units.
To overcome this problem, most frequency inverters switching frequency could be increased to a higher value, which will eliminate the noise problem, but this will introduce Harmonics. Therefore proper design of an installation should be done before using inverters.
To overcome this problem, most frequency inverters switching frequency could be increased to a higher value, which will eliminate the noise problem, but this will introduce Harmonics. Therefore proper design of an installation should be done before using inverters.
Frequency inverters have many advantages and each manufacturer of frequency inverters claims different advantages of their units, this article will cover a couple of basic benefits which we use with most installations.
A fundamental principal of a frequency inverter is to adjust the speed of an electric motor. The basic command frequency for frequency inverters is normally from 0 Hz to 50 Hz, but with the average capability to be adjusted up-to 400 Hz. If the base frequency of a motor is 50 Hz then the final speed will be 8 times the base frequency of the motor with the command frequency set at 400 Hz.
A fundamental principal of a frequency inverter is to adjust the speed of an electric motor. The basic command frequency for frequency inverters is normally from 0 Hz to 50 Hz, but with the average capability to be adjusted up-to 400 Hz. If the base frequency of a motor is 50 Hz then the final speed will be 8 times the base frequency of the motor with the command frequency set at 400 Hz.