Category
- Products
-
- Solar Energy
- FAQ
- Solar Photovoltaic
- Contact us
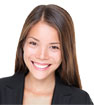
Inverter manufacturer


How to choose inverter for AC motor?
In my opinion the most important consideration of choosing an inverter is the application itself. Inverters are current limited devices and selecting the right frequency inverter requires that the frequency inverter be able to deliver the needed current for all circumstances.
As starting torque is important for its selection we must give details of torque required based on inverter (may be gear, load). Also important is location of the inverter. If it is away from ac motor then we have to provide chokes for impedance. This is generally told by the inverter suppliers. We also need to inform the bypass system for frequency inverter if our application is important from application point of view.
Some applications are as follows:
1. Constant Torque. This is where the torque required to run the load is the same no matter what speed it is running at. For example a conveyor with a 1000 lb load and a 1 foot radius head pulley would require 1000 ft. Lb. of torque at all speeds. Because these applications can be started under full load conditions the rule of thumb is to provide a frequency inverter with 150% overload capacity for 60 seconds in order to overcome the inertia at start up and for overload conditions. Further understanding of the application is required for situation such as an outdoor conveyor that has is fully loaded overnight with a wet gravel load which is now frozen. Starting this load might require 200% or more full load torque, current and HP just to get it running.
2. Variable Torque. This is where the power required to run the driven equipment increases to the cube of the speed. For example centrifugal pumps and fans. Because these applications start with no load and build up to full load they generally do not require more than 100% of full load torque, current and HP. Inverters with 110% overload capacity for 60 seconds can protect the driven equipment in the case of bearing failure etc. This is the type of application where energy savings are usually large. For example if you have a 300HP water cooling tower fan. To get the return water temperature that you desire in August may require full flow of air. In January you may only require 50% air flow and each month may be different. At 80% flow the horse power required would be about 52% providing saving of 48%.
3. Constant Horse Power. This is where the torque required to run the load changes with the process. An example here is a vacuum mixer used to make soap. The operator starts the vacuum mixer and has it running at full speed. He adds water, then other chemicals one after the other. As each chemical is added he reduces the speed but the soap gets thicker and thicker requiring more and more torque. Since the speed is reducing and the torque is increasing the horse power required might be constant or it might even require more horse power at the low speeds. The old variable pitch belt drives were very good for these applications because they provided constant HP from full to half speed.
For example can be applied as a motor-pump, can be attached to a transmission or a gear train, for each application that is intended for the engine, it has to do a study of how consume flow, with this one would know if the inverter should be more robust, also with a detailed study of the application might know why V: F (speed: frequency) to be used when choose an inverter.
The inverter must be in a dry, without heat and humidity, must be in an area that has ventilation, 1.5 meters away from the engine. For greater control of the system "inverter-motor", a connection is made USS (CPU-drive) to a DAQ system with LabView, to keep as a slave to inverter and have a greater vision on the performance of the motor and inverter.
We sell a lot of frequency inverters over the web and therefore have a good idea of peoples shopping behavior. Looking at search traffic, customers usually navigate by application first and then choose a brand or filter by price. If they are using looking for something special (i.e. x number of digital inputs) they use the advanced filters.
Customers will usually choose frequency inverter brands they have used before. These are not always the cheapest brands and not always the best solution for the problem.
In most cases if there is an application or programming issue of the inverter and that some salesman will be hard to reach or he will give you the 1-800 number to tech support and you will be stuck with trying to explain your issue to someone who either has limited field experience or is digging through a manual while on the phone. He is selling a box and should be avoided. Local, trained field personnel from whom you buy your inverter should be primary when considering brand and you should consider the knowledge base of your customer as well. Are they going to properly maintain? Are they trained on the product and is who you are buying from willing to train your customer?
Let's face it, inverters are becoming commodities in the market and usually selected by price rather than any other factor until they get onsite and either don't fit the application or the customer is disturbed because they can't get assistance.
MTBF ratings are arbitrary as they do not take environment into consideration. An inverter in a clean room with a moderate ambient will usually outlast and out perform a frequency inverter in a plant environment that has high ambient with a large particulate issue. Generally, manufacturers produce a 10-15 year MTBF rating but, board level capacitors are only rated at 5 years by their manufacturers. Fans have a much lower rating and would be adjusted due to environment.
My suggestion when selecting manufacturers of inverters, choose from a local authorized service provider for that manufacturer and stay away from anyone who doesn't have a certified frequency inverter specialist on staff.
As starting torque is important for its selection we must give details of torque required based on inverter (may be gear, load). Also important is location of the inverter. If it is away from ac motor then we have to provide chokes for impedance. This is generally told by the inverter suppliers. We also need to inform the bypass system for frequency inverter if our application is important from application point of view.
Some applications are as follows:
1. Constant Torque. This is where the torque required to run the load is the same no matter what speed it is running at. For example a conveyor with a 1000 lb load and a 1 foot radius head pulley would require 1000 ft. Lb. of torque at all speeds. Because these applications can be started under full load conditions the rule of thumb is to provide a frequency inverter with 150% overload capacity for 60 seconds in order to overcome the inertia at start up and for overload conditions. Further understanding of the application is required for situation such as an outdoor conveyor that has is fully loaded overnight with a wet gravel load which is now frozen. Starting this load might require 200% or more full load torque, current and HP just to get it running.
2. Variable Torque. This is where the power required to run the driven equipment increases to the cube of the speed. For example centrifugal pumps and fans. Because these applications start with no load and build up to full load they generally do not require more than 100% of full load torque, current and HP. Inverters with 110% overload capacity for 60 seconds can protect the driven equipment in the case of bearing failure etc. This is the type of application where energy savings are usually large. For example if you have a 300HP water cooling tower fan. To get the return water temperature that you desire in August may require full flow of air. In January you may only require 50% air flow and each month may be different. At 80% flow the horse power required would be about 52% providing saving of 48%.
3. Constant Horse Power. This is where the torque required to run the load changes with the process. An example here is a vacuum mixer used to make soap. The operator starts the vacuum mixer and has it running at full speed. He adds water, then other chemicals one after the other. As each chemical is added he reduces the speed but the soap gets thicker and thicker requiring more and more torque. Since the speed is reducing and the torque is increasing the horse power required might be constant or it might even require more horse power at the low speeds. The old variable pitch belt drives were very good for these applications because they provided constant HP from full to half speed.
For example can be applied as a motor-pump, can be attached to a transmission or a gear train, for each application that is intended for the engine, it has to do a study of how consume flow, with this one would know if the inverter should be more robust, also with a detailed study of the application might know why V: F (speed: frequency) to be used when choose an inverter.
The inverter must be in a dry, without heat and humidity, must be in an area that has ventilation, 1.5 meters away from the engine. For greater control of the system "inverter-motor", a connection is made USS (CPU-drive) to a DAQ system with LabView, to keep as a slave to inverter and have a greater vision on the performance of the motor and inverter.
We sell a lot of frequency inverters over the web and therefore have a good idea of peoples shopping behavior. Looking at search traffic, customers usually navigate by application first and then choose a brand or filter by price. If they are using looking for something special (i.e. x number of digital inputs) they use the advanced filters.
Customers will usually choose frequency inverter brands they have used before. These are not always the cheapest brands and not always the best solution for the problem.
In most cases if there is an application or programming issue of the inverter and that some salesman will be hard to reach or he will give you the 1-800 number to tech support and you will be stuck with trying to explain your issue to someone who either has limited field experience or is digging through a manual while on the phone. He is selling a box and should be avoided. Local, trained field personnel from whom you buy your inverter should be primary when considering brand and you should consider the knowledge base of your customer as well. Are they going to properly maintain? Are they trained on the product and is who you are buying from willing to train your customer?
Let's face it, inverters are becoming commodities in the market and usually selected by price rather than any other factor until they get onsite and either don't fit the application or the customer is disturbed because they can't get assistance.
MTBF ratings are arbitrary as they do not take environment into consideration. An inverter in a clean room with a moderate ambient will usually outlast and out perform a frequency inverter in a plant environment that has high ambient with a large particulate issue. Generally, manufacturers produce a 10-15 year MTBF rating but, board level capacitors are only rated at 5 years by their manufacturers. Fans have a much lower rating and would be adjusted due to environment.
My suggestion when selecting manufacturers of inverters, choose from a local authorized service provider for that manufacturer and stay away from anyone who doesn't have a certified frequency inverter specialist on staff.
Post a Comment:
You may also like: